About Grease Separator Testing Methods: North American and European Standards
- Jan 6, 2021
- 0 Comments
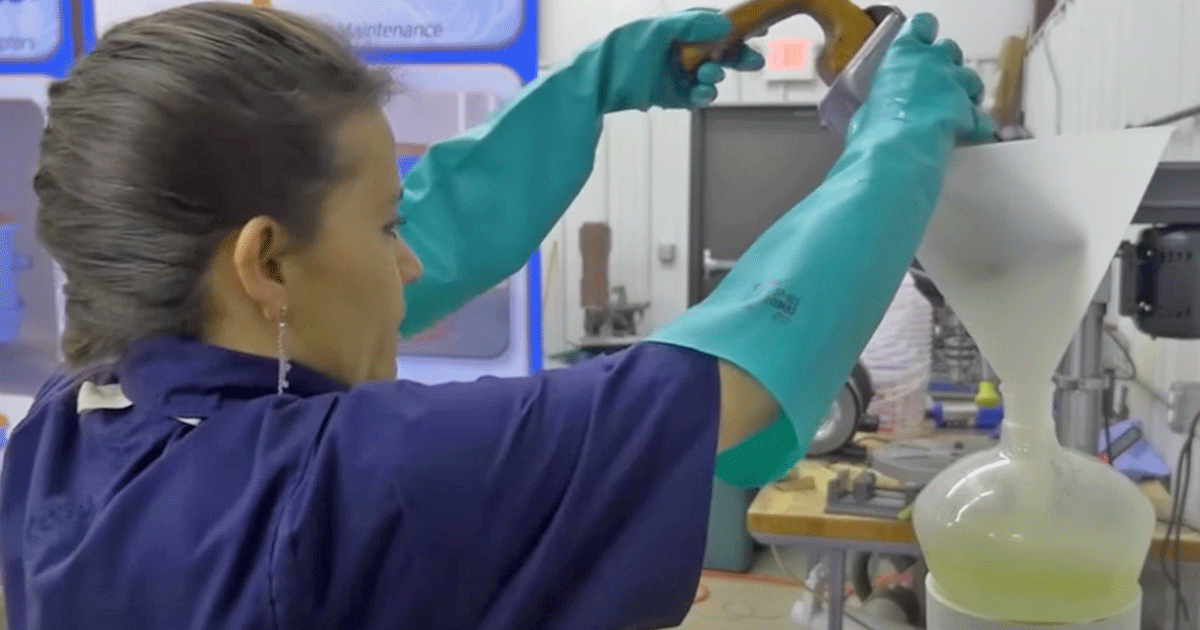
Did you know the North American and European testing standards for certifying grease separators have nothing in common literally?
One is predominately a performance standard, a batch flow test simulating kitchen sink discharge. The other is mostly a design standard, a continuous flow test simulating floor drains receiving oily water flows.
The differences speak to each standard’s backstory:
North American Standards
Canadian B481 and ASME A112.14.3 are derived from the Plumbing and Drainage Institute’s Standard G101: Testing and Rating Procedure for Grease Interceptors. PDI Standard G101 now has the designation Testing and Rating Procedure for Hydro Mechanical Grease Interceptors.
Issued in 1948, PDI G101 was an industry-wide effort during World War II. North American governments sought to capture all sources of animal fats and vegetable oils for use as feedstock in munitions. Most explosives of that era utilized nitroglycerin chemistry. Glycerin is derived from lipids, which is what animal fats and vegetable oils are.
The ASME standard’s roots are clearly based on commercial kitchen operational ware washing practices.
European Standard
Today’s European separator standard EN 1825 evolved from the German Z-54.1-440 Standard. The Z-54.1-440 Standard, in turn, traces to an earlier German standard for oil/water separators in industrial settings, the DIN 4040. Its origins go back to 1935, when it was created by Normenausschuss Wasserwesen (Water Practice Standards Committee), Technical Committee Abscheider. The EN 1825 standard’s roots are based on industrial flow practices.
How Testing for the ASME Standard Works
The ASME A112.14.3 Standard contains 27 pages and is predominately a performance standard. Performance standards state the pass-fail criteria in a numerically measured manner. The appearance, physical size, and design are not stipulated or measured. The performance is the predominant factor evaluated.
The ASME A112.14.3 Standard centers around a batch discharge methodology that replicates a commercial sink filling and emptying into a downstream separator. In the ASME A112.14.3 test, two sinks are filled with 150º F to 160º F (66º C to 71º C) hot water. A loading of hot animal fat (pig lard) representing one pound (0.45kg) of lard to 5 gallons (19L) of water. In effluent terms, 12,500 ppm (mg/l) in Fats, Oils, Grease (FOG) flowing to the downstream grease interceptor.
Each fluid batch release is timed. The standard requires the flow rate not to drop below the separator’s rated flow rate or exceed it by 5% (mathematically shown as nominal flow rate -0%/+5%).
A large holding tank is set downstream of the tested separator. This tank is called the skimming tank, where residual grease passing through the tested grease separator is captured. It’s skimmed between batch runs. Collected grease is sorted by a separatory funnel and weighed. The amount of grease captured downstream determines the tested separator’s grease separation efficiency.
The ASME Standard also has a minimum grease retention performance aspect. For example, a 20 GPM (1.26 l/s) separator must hold a minimum of 40 pounds (18.15 kg) of retained grease while not having less than a cumulative 90% separation efficiency. Additionally, a test segment having less than 80% efficiency is not passing and ends the test.
How Testing for the European Standard Works
The EN 1825 Standard contains 50 pages with considerable emphasis on design standard aspects. The EN 1825 performance test involves a continuous 20-minute flow with fuel oil (diesel fuel) continuously added at a 5 ml per liter of water flow rate. The water is not heated, and its temperature is whatever the supplied water source happens to be that day.
A separator rated at 4 liters per second flow would thus receive 4800 liters of water during the certification test. (Math check: 4 l/s x 5/ml/s x 60 seconds x 20 minutes = 24,000 ml (24 l) of oil and 4l/s x 60 seconds x 20 minutes = 4800 liters)
Oil and water flow continuously for the entire 20-minute test period. The effluent samples are only taken in the last five minutes of the test, using a novel open-face-to-flow weir tube. Five separate 500-ml samples are taken, starting at minute 15 and spaced one minute apart. The five effluent samples are then laboratory tested using infrared spectroscopy or a gas chromatography method. No individual sample can have a value higher than 30 mg/l.
Which Test Is Best?
The North American grease separator standards emulate the batch flow release rhythms of a commercial kitchen’s operation (sink flows, lard, hot water). The European grease interceptor standard emulates an industrial operation's continuous flow character (cold water, fuel oil). Both are valid standards. Both are rigorous. Both tell a lot about the separator being tested.
We have learned a lot from testing our Trapzilla and Big Dipper separators to both the ASME and EN 1825 methods. The ASME’s batch release methodology allows the grease to stratify in the sinks. Thus, the grease is naturally concentrated in the last flow portion exiting the sink drain. This is how a kitchen operates. It’s a valid method for assessing a grease separator.
As flow rates increase, the ASME test is more difficult to pass because of the flows' sheer energy. This energy can affect inlet separator baffle performance and introduce more mechanical mixing of residual grease ahead of the inlet in the piping.
The continuous water and oil feed of the EN 1825 test negates most stratification aspects. Oil is buoyant (less dense than water) and quickly rises to the surface. With a fixed-length pipe between the oil entry/mixing chamber and the downstream separator on the test, naturally rising oil is further adversely precluded as the testing flow rate increases.
I like both tests. Both tests become more difficult to pass with higher flow rates. The ASME A112. 14.3/PDI G101/ CSA B481 methods more closely emulate commercial kitchen flows than the EN 1825. The EN 1825 test answers how well a separator does with oily water continuous flows (no upstream stratification). As a manufacturer, we respect the local codes and standards. It is why we test our products to all applicable standards.
I welcome hearing your thoughts and questions. It is a pretreatment area worth discussing.